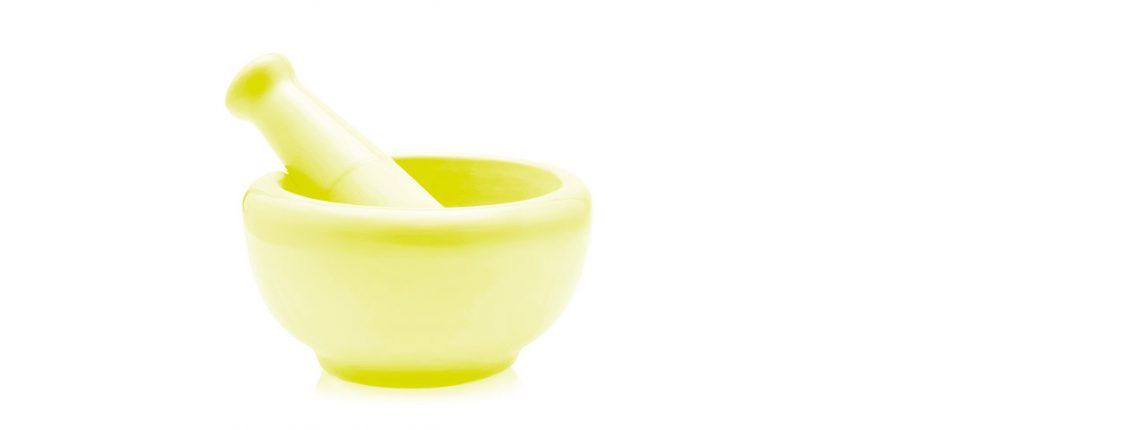
Chemie Geschüttelt, nicht gerührt
Bei vielen chemischen Reaktionen kommen umweltschädliche Lösungsmittel zum Einsatz. Die chemische Industrie erzeugt daher gewaltige Mengen gefährlicher Abfälle. Am besten wäre es, gar keine Lösungsmittel zu verwenden
Nachdem Sie das letzte Mal ein Ei gekocht haben, haben Sie das Wasser, welches ein Vielfaches des Volumens des Eis hatte, sicher weggeschüttet. Grundsätzlich funktionieren so auch die Prozesse in der chemisch-pharmazeutischen Industrie. Um im Bild zu bleiben: Das rohe Ei entspricht den Ausgangsstoffen, das Wasser ist das Lösungsmittel, in dem die Reaktion – das Garwerden des Eis – stattfindet. Das Produkt ist am Ende das gekochte Ei.
In gewaltigen Anlagen – der größte Chemiepark Deutschlands, der ChemCoast Park Brunsbüttel, erstreckt sich beispielsweise über eine Fläche von etwa 2800 Fußballfeldern – werden Chemikalien in Lösungsmitteln gelöst, gerührt, erhitzt und nach der Reaktion wieder abgetrennt. Lösungsmittel machen dabei oft 80 bis 90 Prozent der Gesamtmasse einer Reaktion aus. Das ist problematisch, da es sich dabei meist um toxische und umweltbelastende organische Substanzen handelt, die nicht einmal an der eigentlichen chemischen Reaktion teilnehmen. Diese Mengen werden in den Anlagen erhitzt und bewegt, was große Mengen Energie erfordert, während die Lösungsmittel am Ende als Abfall anfallen.
Doch warum werden diese Lösungsmittel überhaupt verwendet, wenn sie doch an der Reaktion selbst gar nicht teilnehmen und stattdessen Prozesse nur energieintensiver, gefährlicher und umweltschädlicher machen? Die Antwort: Lösungsmittel sind notwendig, um Chemikalien miteinander zu vermischen, Zwischenprodukte zu stabilisieren oder die Hitze der Reaktion abzuführen. Doch dies stimmt nur, wenn man davon ausgeht, dass die gewünschte Reaktion nur möglich ist, indem man Stoffe löst und das Gemisch unter rühren und erhitzen zur Reaktion bringt. In Zeiten steigenden Umweltbewusstseins rücken nun aber nachhaltigere Alternativen in den Fokus. Zum Beispiel die Mechanochemie.
In der Mechanochemie dienen Kugelmühlen als Reaktoren. Die Ausgangsstoffe werden gemeinsam mit Mahlkugeln in Behälter gegeben und bei hohen Frequenzen geschüttelt. Dabei prallen die Kugeln gegeneinander und erzeugen mechanische Energie, welche ihrerseits chemische Reaktionen auslösen kann – und das ganz ohne Lösungsmittel. Im Rahmen unserer Arbeit beschäftigen wir uns mit der Entwicklung nachhaltiger Reaktionen auf Basis der Mechanochemie. Zuletzt untersuchten wir zwei Arten von chemischen Reaktionen: Umlagerungen und photochemische Reaktionen.
Bei Umlagerungen enthalten sowohl Ausgangsstoff als auch Produkt der Reaktion die gleiche Anzahl und Art von Atomen. Lediglich deren Anordnung unterscheidet sich. Umlagerungen sind besonders interessant für die Entwicklung nachhaltiger Synthesen, da alle Bestandteile des Ausgangsstoffes auch für das Produkt verwendet werden und nicht als Neben- oder Abfallprodukte enden.
Wir untersuchten zwei Umlagerungsreaktionen: die „Beckmann-“ und die „Fries-Umlagerung“. Diese Reaktionen sind von Bedeutung für die Herstellung von Funktionsmaterialien oder Arzneistoffen. Prominente Beispiele: Caprolactam und Paracetamol. Caprolactam ist der Ausgangsstoff zur Herstellung der Kunstfaser Perlon und wird jedes Jahr im Millionen-Tonnen-Maßstab produziert. Paracetamol hingegen ist mit über zehn Millionen Packungen pro Jahr eines der meistverkauften Schmerzmittel Deutschlands.
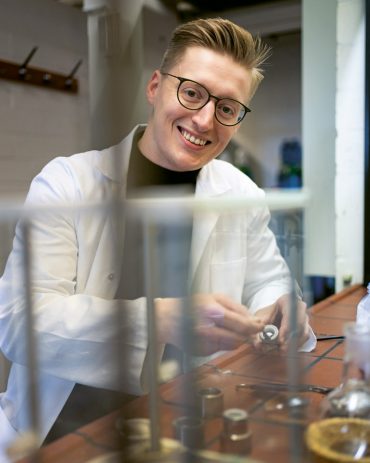
Wir haben eine Vielzahl von Reaktionsparametern untersucht sowie geeignete Katalysatoren und Additive ausgewählt – und konnten schließlich zeigen, dass sich beide Umlagerungen in Kugelmühlen durchführen lassen.
Allerdings eignen sich Kugelmühlen nur bedingt für die Produktion größerer Mengen, wie sie in Industrieprozessen benötigt werden. Daher haben wir unser Verfahren mittels Doppelschneckenextruder (DSE) skaliert. Dabei werden Stoffe durch zwei ineinandergreifende Metallschnecken miteinander vermischt. Dadurch entstehen Scherkräfte, welche die notwendigen mechanischen Energien für eine Reaktion bereitstellen. Mittels DSE gelang es uns, beide Reaktionen in größere Maßstäbe zu übertragen. Konkret konnten wir die erzeugte Abfallmenge in der Beckmann-Umlagerung um etwa 75 Prozent senken, während in der Fries-Umlagerung die Reaktionszeit um 97 Prozent reduziert und gleichzeitig die Ausbeute um mehr als das 1,5-Fache gesteigert wurde. Damit konnten wir nicht nur die ersten Umlagerungsreaktionen mittels DSE überhaupt durchführen. Wir konnten auch zeigen, dass die Mechanochemie eine umweltfreundliche Alternative für die Durchführung dieser wichtigen Reaktionsklasse darstellt.
Wie erwähnt, untersuchten wir neben den Umlagerungen auch photochemische Reaktionen. Dabei handelt es sich um Reaktionen, die durch Licht ausgelöst werden. Dazu gehört auch die Photosynthese, einer der fundamentalen Prozesse in der Natur. Da Sonnenlicht einfach verfügbar ist, können photochemische Reaktionen besonders nachhaltig sein. Wie die meisten Reaktionen werden aber auch photochemische Synthesen meist in Lösungsmitteln durchgeführt. Bei diesem Reaktionstyp ist das sogar besonders problematisch, da eine hohe Verdünnung der Lösung für eine effiziente Bestrahlung und anschließende Reaktion erforderlich ist. Dadurch entstehen bei photochemischen Reaktionen besonders viele Lösungsmittelabfälle, was ihre industrielle Anwendung häufig unattraktiv macht. Eine Durchführung photochemischer Reaktionen im festen Zustand (ohne Lösungsmittel) ist hingegen schwierig, da die notwendige Durchmischung fehlt.
Unser Ziel war daher, Mechanochemie und Photochemie zu vereinen. In diesen photo-mechanochemischen Reaktionen könnte Licht die Reaktionen antreiben, während die Vermahlung in einer Kugelmühle die notwendige Vermischung im festen Zustand ermöglicht. Jedoch gab es nahezu keine Arbeiten auf diesem Gebiet – was daran liegt, dass geeignetes Equipment schwer zu finden ist: Das Reaktionsgefäß muss einerseits lichtdurchlässig sein, um die photochemischen Reaktionen zu ermöglichen, und andererseits den enormen mechanischen Kräften einer Kugelmühle standhalten.
Am Anfang unserer Experimente stand daher der Bau eines Photoreaktors aus starken LEDs, der die Bestrahlung der Kugelmühle ermöglichte, sowie von durchsichtigen Behältern für die Reaktion. Diese bestanden aus Quarzglasröhren mit Kunststoffverschlüssen. In Kombination mit weichen Polymermahlkugeln konnten wir die ersten beiden Reaktionen in einer Kugelmühle unter Bestrahlung mit UV-Licht durchführen.
Wir untersuchten dabei Reaktionen zur Synthese von Nanographenen. Diese Verbindungen sind etwa bei der Herstellung von OLEDs von Bedeutung – organischen Leuchtdioden, die in hochauflösenden Bildschirmen verwendet werden. Aufgrund ihrer Größe und geringen Polarität sind Nanographene schwer löslich und mit klassischen Methoden entsprechend schwer zugänglich. Wir konnten mit der von uns entwickelten Technik eine Zahl von Nanographenen in guten Ausbeuten erzeugen. Im Gegensatz zur konventionellen Reaktion in Lösung reduzierte sich die Reaktionszeit um 56 Prozent, der Energiebedarf um 78 Prozent und die Lösungsmittelmenge sogar um 98 Prozent.
Die Mechanochemie bietet enormes Potenzial bei der Entwicklung nachhaltiger chemischer Reaktionen – auch wenn die eindrucksvollen Einsparungen gegenwärtig hauptsächlich im Labormaßstab erzielt werden. Doch haben sich weltweit bereits einige junge Firmen der Mechanochemie verschrieben. Auch das Interesse etablierter Unternehmen an dieser Technik wächst. Perspektivisch dürfte sich die Mechanochemie zunächst in Industriezweigen mit geringerer Produktionsmenge wie der Herstellung von Arzneistoffen oder Spezialchemikalien durchsetzen, da hier geringere Investitionen seitens der Industrie notwendig sind. Langfristig könnte das Verfahren – auch unter den steigenden Anforderungen an nachhaltige Prozesse – Anwendung in größeren Maßstäben finden. Auch wenn die Mechanochemie nicht alle der herkömmlichen Prozesse ersetzen wird, kann sie den Anteil nachhaltiger Produktionen deutlich steigern.
Zum Thema
Die Mühlen mahlen unermüdlich
Die chemische Industrie und die globalen Ziele für nachhaltige Entwicklung
Im „Bericht über gefährliche Abfälle nach Erzeugergruppen“ des deutschen Umweltbundesamtes steht, dass in der Chemie- und Pharmaindustrie über fünf Prozent der gefährlichen Abfälle (2019) und fast zwölf Prozent des gesamten Abwassers der deutschen Wirtschaft (2016) anfielen. Überdies habe die Branche im Jahr 2019 etwa zehn Prozent der gesamten Primärenergie Deutschlands verbraucht. Das sind beträchtliche Anteile, die zugleich ein wichtiges Potenzial für mehr Nachhaltigkeit bergen.
Zum Beispiel mithilfe der Mechanochemie, die so alt ist wie der Mensch – nein, noch viel älter. Denn Druck und Temperatur sind ja auch die wichtigsten geologischen Kräfte. Sie können tief im Erdmantel aus Graphit Diamanten entstehen lassen. Wie lange der Mensch das Verfahren nutzt, ist unbekannt. Überliefert ist ein Büchlein mit dem Titel „De lapidibus“ –„Über die Steine“. Der griechische Naturforscher Theophrastos von Eresos schildert darin, wie er um 315 v. Chr. das Mineral Zinnober in einem Kupfermörser zerkleinerte und auf diese Weise reines Quecksilber gewann.
Noch funktionieren die meisten mechanochemischen Prozesse nicht in großem Maßstab. So ist ein Mörser oder eine Mühle auf dem Labortisch noch immer bei Weitem effizienter als eine Kugelmühle, die den industriellen Bedarf decken muss. Dass dies eines Tages gelingt, stellt aber niemand infrage. Bei der Entwicklung locken im Übrigen nicht nur umweltfreundlichere Verfahren. Denn zu den Vorteilen der Mechanochemie gehören neben dem Verzicht auf Lösungsmittel auch niedrige Kosten und ein geringer Energieverbrauch – mehr Effizienz also. Die Mechanochemie kann ein Beispiel dafür sein, dass Investitionen in mehr Nachhaltigkeit nicht mehr, sondern langfristig weniger Geld kosten. — J. Schüring